MicroNet TMR® Control System
Key words:
Classification:
Product Introduction
Applications
The MicroNet TMR®(triple modular redundant) controller is a state-of-the-art digital control platform designed to reliably control and protect steam turbines, gas turbines, and compressor trains used in system-critical applications where the chance of a safety issues or large economic losses may be possible. The MicroNet TMR’s 2-out-of-3 voting architecture ensures that correct decisions are made, correct responses are performed, and the prime mover continues to safely operate with or without any single-point failure. This controller’s robustness, accuracy, and availability make it the choice of turbine and compressor OEMs and operators.
The MicroNet TMR’s superior architecture and diagnostic coverage combine to create a system with 99.999% availability and reliability. The MicroNet TMR can be applied as a component of protection and safety systems to allow the overall system to meet IEC61508 SIL-3 compliance standards. IEC61508 calculations and application assistance are available upon request.
Typical MicroNet TMR application experience and use:
• Refrigeration Compressors (Ethylene, Propylene)
• Methane and Syn Gas Compressors
• Gas Cracker Compressors
• Charge Gas Compressors
• Hydrogen Recycle Compressors
• Critical Turbine Generator Sets
• Turbine Safety Systems
Description
The MicroNet TMR control platform utilizes a robust rack-mounted chassis with online replaceable I/O modules and triple modular architecture to achieve its 99.999% availability. This triple modular redundant based system consists of three isolated kernel sections (A, B, C) housed within the platform’s compact chassis. Each kernel section includes its own CPU, CPU power supply, and up to four I/O modules. The I/O modules can be used for simplex I/O, redundant I/O, triple redundant I/O, or any redundancy combination. I/O expandability is performed via additional system chassis or through distributed I/O.
This platform’s high-density modules and integrated application program provide first-out indication for monitored system events to reduce troubleshooting time. These purpose-built modules time-stamp discrete events within 1 millisecond and analog events within 5 milliseconds. The MicroNet TMR uses two power supplies, each of which powers the control from a separate power source. Inside each power supply are three independent power converters, one for each CPU and I/O section. This triplicate power architecture provides maximum protection against single or multi-point hardware failures
The control’s special TMR Discrete I/O modules are designed for use in critical discrete circuits. This module accepts discrete inputs and distributes these inputs to each of the separate kernel sections, as well as output relay-based contacts to drive discrete application logic. The module’s special TMR outputs utilize a six-relay configuration and integrated latent fault detection logic to allow the failure of any one or in some cases two relays without affecting the integrity of the output contact. This type of architecture allows routine relay testing to be performed as well as on-line reparability, without affecting the integrity of the output or system.
Designed as a turbine control system, the MicroNet TMR controller’s actuator driver modules are designed to interface with proportional or integrating turbine valve servos using single or dual redundant coils, with AC or DC feedback position sensors. The MicroNet TMR control can accommodate any combination of Woodward standard MicroNet I/O modules to provide maximum application flexibility.
Available Inputs and Outputs include:
• Magnetic pickups (MPUs) and proximity probes
• Discrete I/O
• Analog I/O
• Thermocouple inputs
• Resistance temperature devices (RTDs)
• Proportional and integrating actuator drivers (integrated AC and DC position inputs)
• Ethernet and Serial communications
Fault Tolerance
Each of the MicroNet TMR controller’s kernel sections individually monitors all input data, performs all application calculations, and generates all output values
and responses. This control’s architecture allows it to operate with any single point of failure, without shutting down. Architected for reliability and safety, the system’s CPU fault tolerance logic of 3-2-0 allows the control to function normally with any CPU module failed or removed, and ensures a safe shutdown with multiple CPU failures. An analog I/O fault tolerance logic of 3-2-1-0 allows the control to function normally with any one or two analog modules failed or removed. A discrete I/O fault tolerance logic of 3-2-1-0 allows the control to function normally with any one or two discrete modules failed or removed. A power supply fault tolerance logic of 2-1-0 allows the control to function normally with any one power supply failed or removed.
Each kernel CPU module runs the identical software program, in “lock-step” with the other two CPUs. All inputs from each kernel are distributed to the other two kernels. For each sensed input, each CPU compares its read value with the value the other two CPUs read before outputting a signal to the application software. All CPUs use the same voted input signals in the same application calculations to generate the same outputs.
All output values are then exchanged between kernels, the results are voted, and the appropriate value is output
Programming
The MicroNet TMR control system provides an IEC1131-3 environment for programming. Application code is generated by use of Woodward’s GAP™
Graphical Application Programming environment or Woodward’s Ladder Logic programming environment.
• Function Block Programming — through Woodward GAP
• Sequential Function Chart Programming — through Woodward GAP
• Ladder Logic Programming — through Woodward Ladder Logic Programmer
The MicroNet TMR operating system, together with GAP, produces a very powerful control environment designed for control and protection of turbines and compressors. Woodward’s unique scan rate structure ensures that control functions will execute deterministically at defined scan rates, with critical control loops able to be processed within 5 milliseconds. Accurate speed and speed acceleration and deceleration rates are sensed using a sampling rate of 100 microseconds. These ultra-fast sampling and response rates allow the controller to adequately respond to system transients, failures, or safety events.
Communications
The MicroNet TMR platform’s open-architecture allows users to easily interface with plant DCSs, HMIs, and distributed I/O devices for system operation, as well as control programming and service. Multiple communication ports and protocols are available for system communications, allowing users to select their desired communication method and level of communication redundancy. MicroNet-to-DCS communications have been performed and qualified with all major DCS vendors. The following communication ports are available for use:
• Ethernet ports (10/100 BaseT)
• RS-232/-422/-485 Serial ports
• LON network for LinkNet®Distributed I/O Modules
Protocols Supported:
• Modbus®* (Serial or Ethernet)
• Ethernet TCP/IP & UDP
• OPC (OLE for Process Control)
• Printer Drivers, Modems, Data Loggers *—Modbus is a trademark of Schneider Automation Inc.
Woodward also offers a suite of software service-tools to simplify system troubleshooting and service. These tools provide high-speed (5 milliseconds) operational and analytical information such as graphical display of operating data, historical trending, event logging, X-Y plotting, system overviews, calibration pages, and other functions.
Expandability
The MicroNet TMR platform is expandable into additional expansion chassis as required by the system size, and will support any mix of I/O, including networked and/or distributed I/O. Redundant “Real-Time Ethernet” networks are utilized between main and expansion chassis to ensure a fast and reliable communications. Expansion chassis are available in 6-, 8-, 12-, or 14-slot models. This TMR architecture allows all remote I/O points to be automatically shared with each kernel CPU, increasing system robustness and availability
Specifications
Operating Conditions
Temperature
0 to 55 °C (32 to 131 °F) ambient air temperature range
Shock
US MIL-STD-810C, method 516.2-1, procedure 1B
Vibration
Lloyd’s ENV2 test #1
Emissions *
EN61000-6-4
Immunity *
EN61000-6-2
Certifications *
CE, UL/cUL (Class I, Division 2), LR for ENV1 & ENV2, ABS, GOST-R
MicroNet TMR Chassis —18 slot chassis
Bulkhead mounted or adaptable to 19” (483 mm) rack mount back panel.
Control Chassis Dimensions
18.8” wide x 14.3” high x 12.1” deep (478 mm wide x 363 mm high x 307 mm deep)
Control Chassis Weight
55 lb (25 kg)
Power Chassis Dimensions
6.4” wide x 14.3” high x 12.1” deep (163 mm wide x 363 mm high x 307 mm deep)
Power Chassis Weight
16 lb (7 kg)
Power Supply Input Options
18–36 Vdc, 100–150 Vdc, 88–132 Vac (47–63 Hz), 180–264 Vac (47–63 Hz)
*—Specifications apply to most components and modules. Some certifications may be pending. Contact Woodward for further information. Do not
use the drawings in this specification for construction.
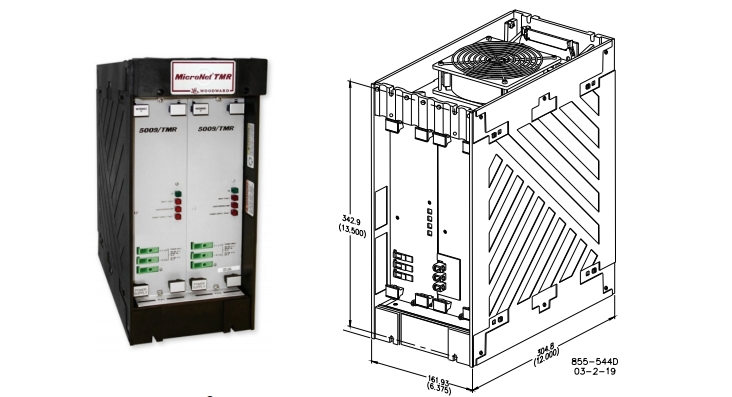
MicroNet TMR® Power Supply Chassis (Do not use for construction)
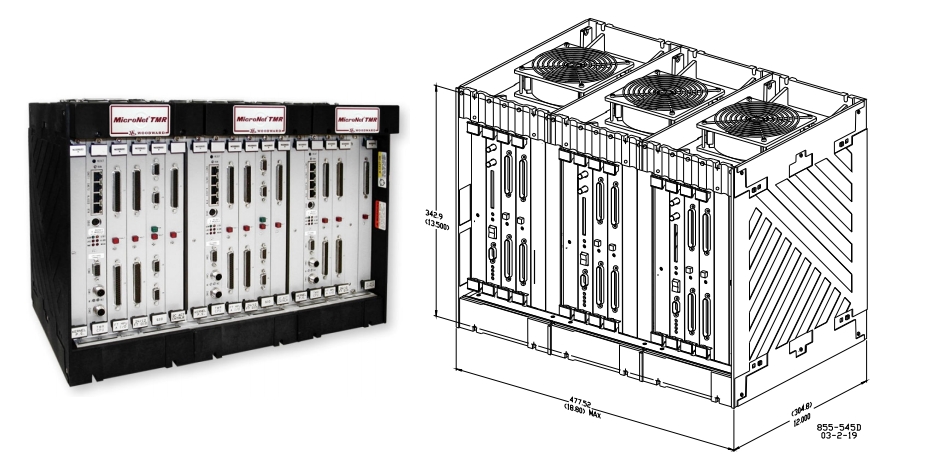
MicroNet TMR Control Chassis (Do not use for construction)
Previous:
The next one:
Related Products
Product Consulting
If you are interested in our products, please leave your email, we will contact you as soon as possible, thank you!